Siliziumnitrid (Si₃N₄)-Keramiken besitzen als fortschrittliche Strukturkeramik hervorragende Eigenschaften wie hohe Temperaturbeständigkeit, hohe Festigkeit, hohe Zähigkeit, hohe Härte, Kriechfestigkeit, Oxidationsbeständigkeit und Verschleißfestigkeit. Darüber hinaus bieten sie eine gute Temperaturwechselbeständigkeit, dielektrische Eigenschaften, eine hohe Wärmeleitfähigkeit und eine hervorragende Übertragungsleistung bei hochfrequenten elektromagnetischen Wellen. Aufgrund dieser herausragenden umfassenden Eigenschaften werden sie häufig in komplexen Strukturbauteilen eingesetzt, insbesondere in der Luft- und Raumfahrt und anderen High-Tech-Bereichen.
Da es sich jedoch um eine Verbindung mit starken kovalenten Bindungen handelt, weist Si₃N₄ eine stabile Struktur auf, die das Sintern auf eine hohe Dichte allein durch Festkörperdiffusion erschwert. Um das Sintern zu fördern, werden Sinterhilfsmittel wie Metalloxide (MgO, CaO, Al₂O₃) und Seltenerdoxide (Yb₂O₃, Y₂O₃, Lu₂O₃, CeO₂) zugesetzt, um die Verdichtung über einen Flüssigphasen-Sintermechanismus zu erleichtern.
Derzeit schreitet die globale Halbleiterbauelementtechnologie in Richtung höherer Spannungen, größerer Ströme und größerer Leistungsdichten voran. Die Forschung zu Methoden zur Herstellung von Si₃N₄-Keramik ist umfangreich. In diesem Artikel werden Sinterprozesse vorgestellt, die die Dichte und die umfassenden mechanischen Eigenschaften von Siliziumnitridkeramik effektiv verbessern.
Gängige Sintermethoden für Si₃N₄-Keramik
Vergleich der Leistung von Si₃N₄-Keramiken, die mit verschiedenen Sintermethoden hergestellt wurden
1. Reaktives Sintern (RS):Reaktives Sintern war die erste Methode zur industriellen Herstellung von Si₃N₄-Keramik. Es ist einfach, kostengünstig und ermöglicht die Bildung komplexer Formen. Der Produktionszyklus ist jedoch lang, was einer Produktion im industriellen Maßstab nicht förderlich ist.
2. Druckloses Sintern (PLS):Dies ist der grundlegendste und einfachste Sinterprozess. Es erfordert jedoch hochwertige Si₃N₄-Rohstoffe und führt oft zu Keramiken mit geringerer Dichte, erheblicher Schrumpfung und einer Tendenz zur Rissbildung oder Verformung.
3. Heißpresssintern (HP):Die Anwendung eines einachsigen mechanischen Drucks erhöht die Antriebskraft beim Sintern und ermöglicht die Herstellung dichter Keramiken bei Temperaturen, die 100–200 °C niedriger sind als beim drucklosen Sintern. Dieses Verfahren wird typischerweise zur Herstellung relativ einfacher blockförmiger Keramiken verwendet, es ist jedoch schwierig, die Dicken- und Formanforderungen für Substratmaterialien zu erfüllen.
4. Spark-Plasma-Sintern (SPS):SPS zeichnet sich durch schnelles Sintern, Kornverfeinerung und reduzierte Sintertemperaturen aus. SPS erfordert jedoch erhebliche Investitionen in die Ausrüstung, und die Herstellung von Si₃N₄-Keramik mit hoher Wärmeleitfähigkeit mittels SPS befindet sich noch im experimentellen Stadium und wurde noch nicht industrialisiert.
5. Gasdrucksintern (GPS):Durch die Anwendung von Gasdruck verhindert diese Methode die Zersetzung der Keramik und den Gewichtsverlust bei hohen Temperaturen. Es ist einfacher, hochdichte Keramik herzustellen und ermöglicht eine Serienfertigung. Allerdings ist es mit einem einstufigen Gasdruck-Sinterverfahren schwierig, Strukturbauteile mit gleichmäßiger innerer und äußerer Farbe und Struktur herzustellen. Der Einsatz eines zweistufigen oder mehrstufigen Sinterprozesses kann den intergranularen Sauerstoffgehalt erheblich reduzieren, die Wärmeleitfähigkeit verbessern und die Gesamteigenschaften verbessern.
Allerdings hat die hohe Sintertemperatur des zweistufigen Gasdrucksinterns dazu geführt, dass sich frühere Forschungen hauptsächlich auf die Herstellung von Si₃N₄-Keramiksubstraten mit hoher Wärmeleitfähigkeit und Biegefestigkeit bei Raumtemperatur konzentrierten. Die Forschung zu Si₃N₄-Keramiken mit umfassenden mechanischen Eigenschaften und mechanischen Hochtemperatureigenschaften ist relativ begrenzt.
Zweistufiges Gasdruck-Sinterverfahren für Si₃N₄
Yang Zhou und Kollegen von der Technischen Universität Chongqing verwendeten ein Sinterhilfssystem aus 5 Gew.-% Yb₂O₃ + 5 Gew.-% Al₂O₃, um Si₃N₄-Keramik herzustellen, indem sie sowohl einstufige als auch zweistufige Gasdrucksinterprozesse bei 1800 °C verwendeten. Die durch den zweistufigen Sinterprozess hergestellten Si₃N₄-Keramiken hatten eine höhere Dichte und insgesamt bessere mechanische Eigenschaften. Im Folgenden werden die Auswirkungen von einstufigen und zweistufigen Gasdrucksinterprozessen auf die Mikrostruktur und die mechanischen Eigenschaften von Si₃N₄-Keramikkomponenten zusammengefasst.
Dichte Der Verdichtungsprozess von Si₃N₄ umfasst typischerweise drei Stufen mit Überlappungen zwischen den Stufen. Die erste Stufe, die Partikelumlagerung, und die zweite Stufe, die Auflösungsfällung, sind die kritischsten Stufen für die Verdichtung. Eine ausreichende Reaktionszeit in diesen Stufen verbessert die Probendichte erheblich. Wenn die Vorsintertemperatur für den zweistufigen Sinterprozess auf 1600 °C eingestellt wird, bilden β-Si₃N₄-Körner ein Gerüst und erzeugen geschlossene Poren. Nach dem Vorsintern fördert weiteres Erhitzen unter hoher Temperatur und Stickstoffdruck das Fließen und Füllen der flüssigen Phase, was dazu beiträgt, geschlossene Poren zu beseitigen und die Dichte der Si₃N₄-Keramik weiter zu verbessern. Daher weisen die durch das zweistufige Sinterverfahren hergestellten Proben eine höhere Dichte und relative Dichte auf als die durch einstufiges Sintern hergestellten Proben.
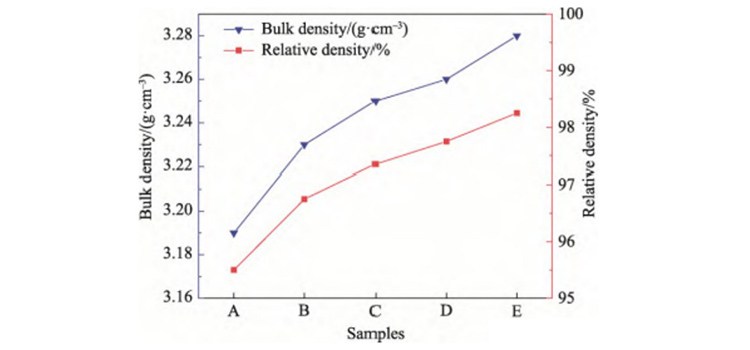
Phase und Mikrostruktur Beim einstufigen Sintern ist die für die Partikelumlagerung und Korngrenzendiffusion verfügbare Zeit begrenzt. Beim zweistufigen Sinterprozess wird der erste Schritt bei niedriger Temperatur und niedrigem Gasdruck durchgeführt, was die Umlagerungszeit der Partikel verlängert und zu größeren Körnern führt. Anschließend wird die Temperatur auf die Hochtemperaturstufe erhöht, wo die Körner durch den Ostwald-Reifungsprozess weiter wachsen und hochdichte Si₃N₄-Keramik entstehen.
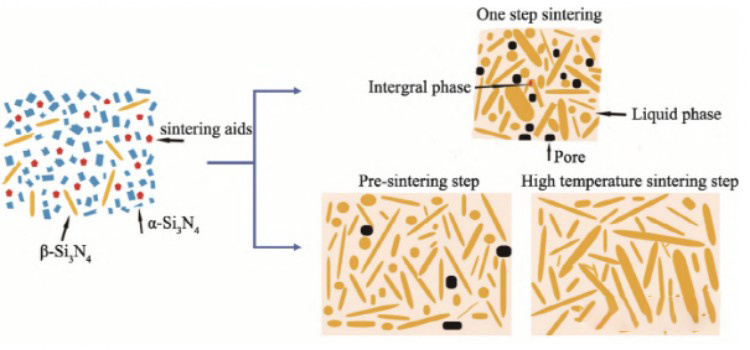
Mechanische Eigenschaften Die Erweichung der intergranularen Phase bei hohen Temperaturen ist der Hauptgrund für die verringerte Festigkeit. Beim einstufigen Sintern entstehen durch abnormales Kornwachstum kleine Poren zwischen den Körnern, was eine deutliche Verbesserung der Hochtemperaturfestigkeit verhindert. Beim zweistufigen Sinterprozess erhöhen jedoch die gleichmäßig in den Korngrenzen verteilte Glasphase und die gleichmäßig großen Körner die interkristalline Festigkeit, was zu einer höheren Biegefestigkeit bei hohen Temperaturen führt.
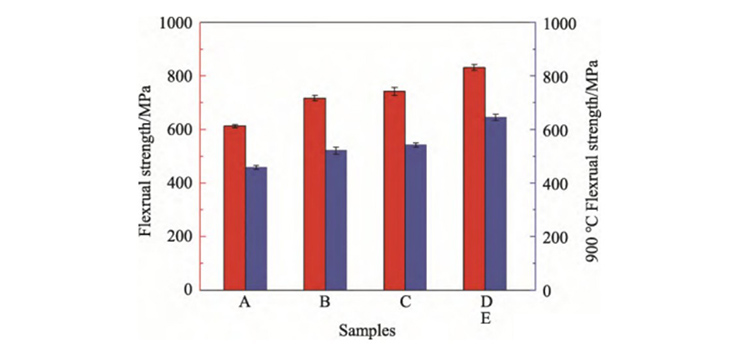
Zusammenfassend lässt sich sagen, dass längeres Halten während des Sinterns in einem Schritt die innere Porosität effektiv reduzieren und eine gleichmäßige innere Farbe und Struktur erreichen kann, aber möglicherweise zu abnormalem Kornwachstum führt, das bestimmte mechanische Eigenschaften verschlechtert. Durch den Einsatz eines zweistufigen Sinterprozesses – Vorsintern bei niedriger Temperatur zur Verlängerung der Partikelumlagerungszeit und Halten bei hoher Temperatur zur Förderung eines gleichmäßigen Kornwachstums – entsteht eine Si₃N₄-Keramik mit einer relativen Dichte von 98,25 %, einer gleichmäßigen Mikrostruktur und hervorragenden umfassenden mechanischen Eigenschaften kann erfolgreich vorbereitet werden.
Name | Substrat | Zusammensetzung der Epitaxieschicht | Epitaktischer Prozess | Epitaxiemedium |
Homoepitaxiales Silizium | Si | Si | Dampfphasenepitaxie (VPE) | SiCl4+H2 |
Silizium-Heteroepitaxie | Saphir oder Spinell | Si | Dampfphasenepitaxie (VPE) | SiH₄+H₂ |
GaAs-Homöepitaxie | GaAs | GaAs GaAs | Dampfphasenepitaxie (VPE) | AsCl₃+Ga+H₂ (Ar) |
GaAs | GaAs GaAs | Molekularstrahlepitaxie (MBE) | Ga+As | |
GaAs-Heteroepitaxie | GaAs GaAs | GaAlAs/GaAs/GaAlAs | Flüssigphasenepitaxie (LPE) Dampfphase (VPE) | Ga+Al+CaAs+ H2 Ga+AsH3+PH3+CHl+H2 |
GaP-Homöepitaxie | Lücke | GaP(GaP;N) | Flüssigphasenepitaxie (LPE) Flüssigphasenepitaxie (LPE) | Ga+GaP+H2+(NH3) Ga+GaAs+GaP+NH3 |
Übergitter | GaAs | GaAlAs/GaAs (Zyklus) | Molekularstrahlepitaxie (MBE) MOCVD | Ca,As,Al GaR₃+AlR3+AsH3+H2 |
InP-Homöepitaxie | InP | InP | Dampfphasenepitaxie (VPE) Flüssigphasenepitaxie (LPE) | PCl3+In+H2 In+InAs+GaAs+InP+H₂ |
Si/GaAs-Epitaxie | Si | GaAs | Molekularstrahlepitaxie (MBE) MOGVD | Ga、As GaR₃+AsH₃+H₂ |
Zeitpunkt der Veröffentlichung: 24. Dezember 2024