Die Beschichtungsverfahren für Fotolack werden im Allgemeinen in Schleuderbeschichtung, Tauchbeschichtung und Walzenbeschichtung unterteilt, wobei Schleuderbeschichtung am häufigsten verwendet wird. Beim Schleuderbeschichten wird Fotolack auf das Substrat getropft und das Substrat kann mit hoher Geschwindigkeit gedreht werden, um einen Fotolackfilm zu erhalten. Anschließend kann durch Erhitzen auf einer Heizplatte ein fester Film erhalten werden. Die Schleuderbeschichtung eignet sich für die Beschichtung von ultradünnen Filmen (ca. 20 nm) bis hin zu dicken Filmen von ca. 100 µm. Seine Eigenschaften sind gute Gleichmäßigkeit, gleichmäßige Filmdicke zwischen den Wafern, wenige Defekte usw. und es kann ein Film mit hoher Beschichtungsleistung erhalten werden.
Schleuderbeschichtungsverfahren
Beim Schleuderbeschichten bestimmt die Hauptrotationsgeschwindigkeit des Substrats die Schichtdicke des Fotolacks. Der Zusammenhang zwischen der Rotationsgeschwindigkeit und der Filmdicke ist wie folgt:
Spin=kTn
In der Formel ist Spin die Rotationsgeschwindigkeit; T ist die Filmdicke; k und n sind Konstanten.
Faktoren, die den Spin-Coating-Prozess beeinflussen
Obwohl die Filmdicke durch die Hauptrotationsgeschwindigkeit bestimmt wird, hängt sie auch von der Raumtemperatur, der Luftfeuchtigkeit, der Viskosität des Fotolacks und dem Fotolacktyp ab. Der Vergleich verschiedener Arten von Photoresist-Beschichtungskurven ist in Abbildung 1 dargestellt.
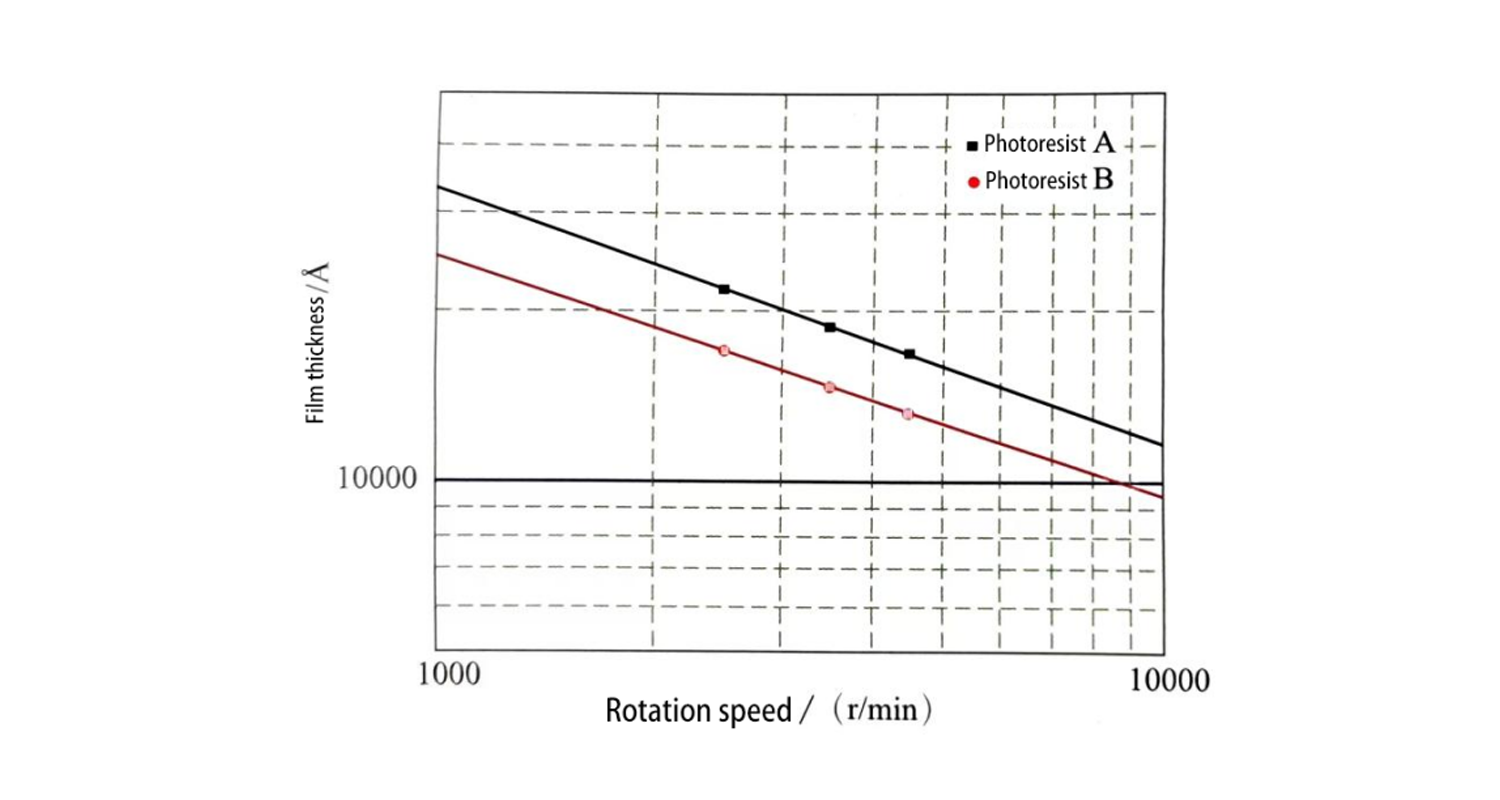
Abbildung 1: Vergleich verschiedener Arten von Photoresist-Beschichtungskurven
Der Einfluss der Hauptrotationszeit
Je kürzer die Hauptrotationszeit ist, desto dicker ist die Filmdicke. Je länger die Hauptrotationszeit ist, desto dünner wird der Film. Bei mehr als 20 Sekunden bleibt die Filmdicke nahezu unverändert. Daher wird die Hauptrotationszeit üblicherweise mit mehr als 20 Sekunden gewählt. Der Zusammenhang zwischen der Hauptrotationszeit und der Filmdicke ist in Abbildung 2 dargestellt.
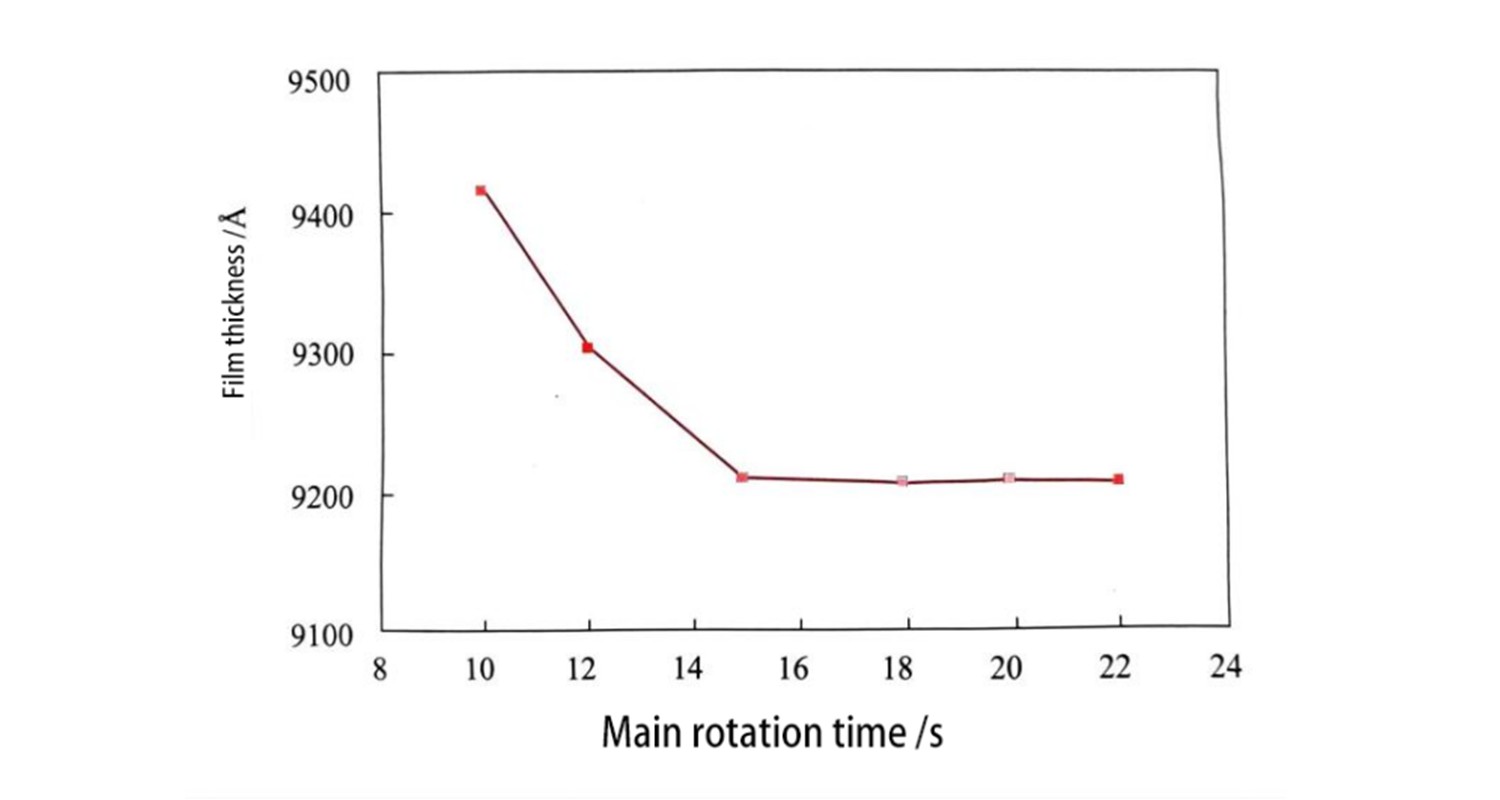
Abbildung 2: Zusammenhang zwischen Hauptrotationszeit und Filmdicke
Wenn der Fotolack auf das Substrat getropft wird, beeinflusst die Rotationsgeschwindigkeit des Substrats während des Auftropfens die endgültige Filmdicke, auch wenn die nachfolgende Hauptrotationsgeschwindigkeit dieselbe ist. Die Dicke des Photoresistfilms nimmt mit zunehmender Rotationsgeschwindigkeit des Substrats während des Auftropfens zu, was auf den Einfluss der Lösungsmittelverdunstung zurückzuführen ist, wenn der Photoresist nach dem Auftropfen entfaltet wird. Abbildung 3 zeigt den Zusammenhang zwischen der Filmdicke und der Hauptrotationsgeschwindigkeit bei unterschiedlichen Substratrotationsgeschwindigkeiten während des Abtropfens des Fotolacks. Aus der Abbildung ist ersichtlich, dass sich die Filmdicke mit zunehmender Rotationsgeschwindigkeit des tropfenden Substrats schneller ändert und der Unterschied im Bereich mit niedrigerer Hauptrotationsgeschwindigkeit deutlicher ist.
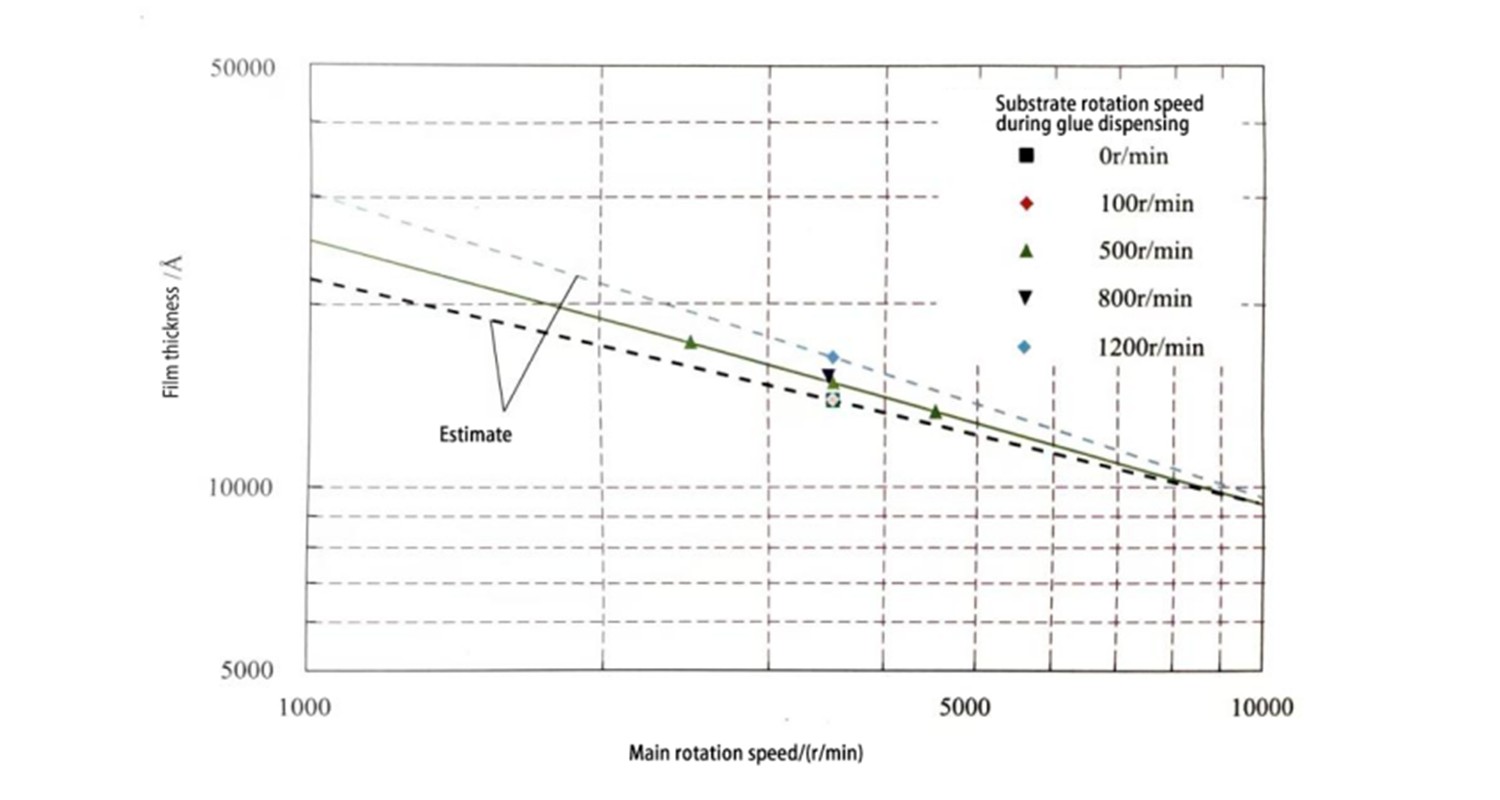
Abbildung 3: Zusammenhang zwischen Filmdicke und Hauptrotationsgeschwindigkeit bei unterschiedlichen Substratrotationsgeschwindigkeiten während der Fotolackdosierung
Einfluss der Luftfeuchtigkeit beim Beschichten
Mit abnehmender Luftfeuchtigkeit nimmt die Filmdicke zu, da die Abnahme der Luftfeuchtigkeit die Verdunstung des Lösungsmittels fördert. Die Schichtdickenverteilung ändert sich jedoch nicht wesentlich. Abbildung 4 zeigt den Zusammenhang zwischen Luftfeuchtigkeit und Schichtdickenverteilung während der Beschichtung.
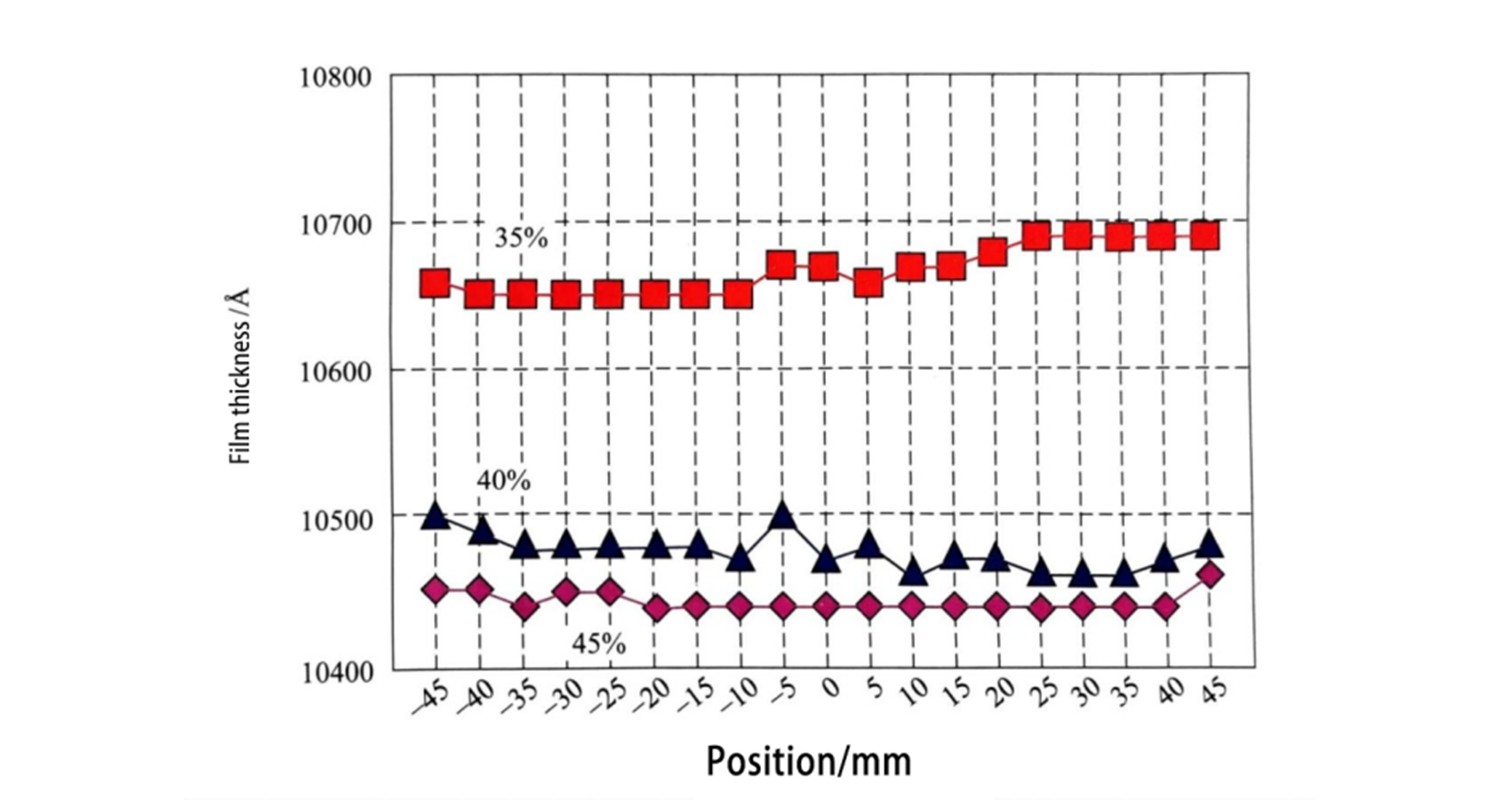
Abbildung 4: Zusammenhang zwischen Luftfeuchtigkeit und Schichtdickenverteilung während der Beschichtung
Temperatureinfluss beim Beschichten
Wenn die Innentemperatur steigt, nimmt die Filmdicke zu. Aus Abbildung 5 ist ersichtlich, dass sich die Dickenverteilung des Fotolackfilms von konvex zu konkav ändert. Die Kurve in der Abbildung zeigt auch, dass die höchste Gleichmäßigkeit erreicht wird, wenn die Innentemperatur 26 °C und die Fotolacktemperatur 21 °C beträgt.
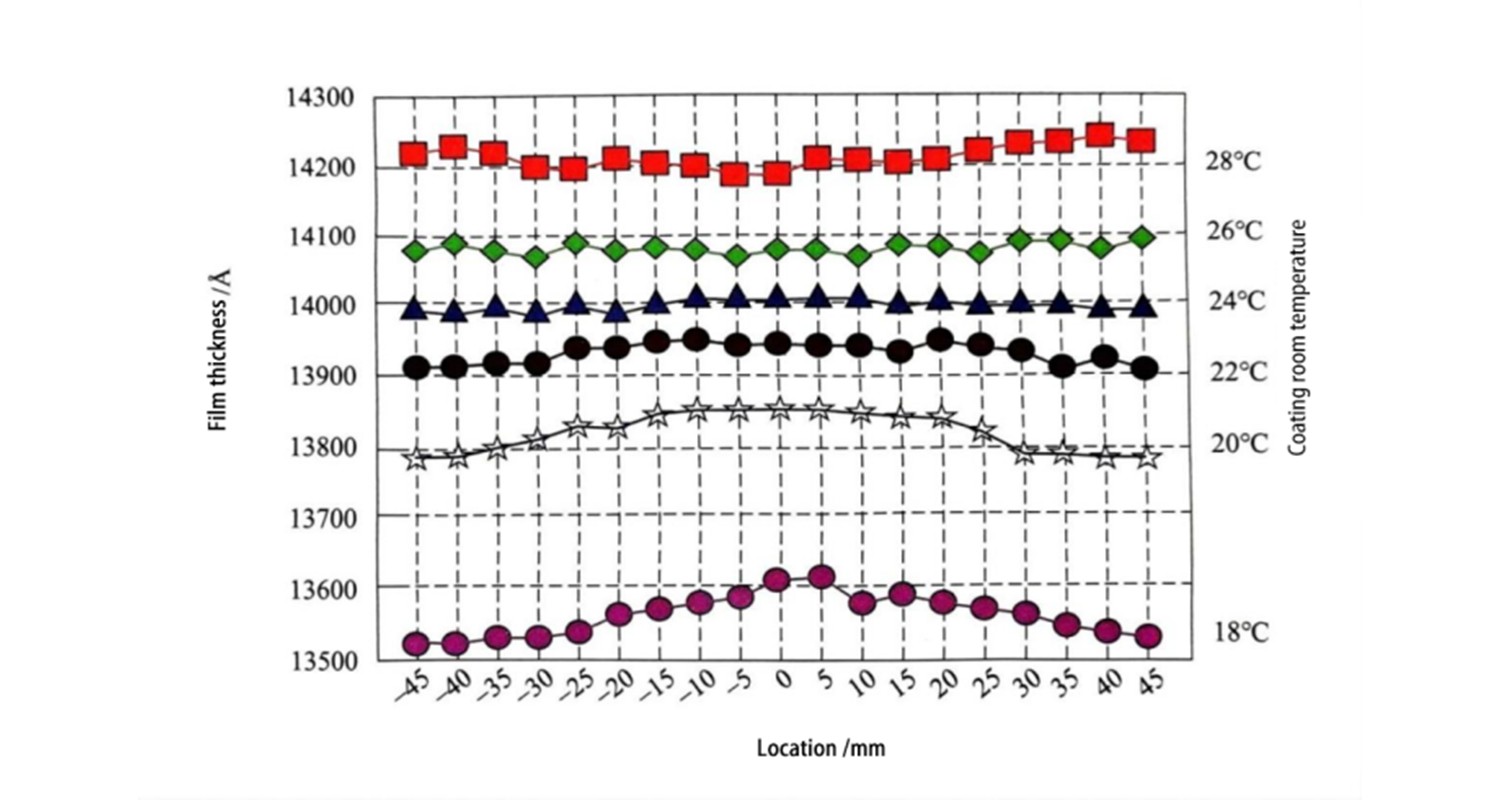
Abbildung 5: Zusammenhang zwischen Temperatur und Schichtdickenverteilung während der Beschichtung
Einfluss der Abgasgeschwindigkeit beim Beschichten
Abbildung 6 zeigt den Zusammenhang zwischen Abgasgeschwindigkeit und Filmdickenverteilung. Ohne Abgas zeigt sich, dass die Mitte des Wafers dazu neigt, dicker zu werden. Durch Erhöhen der Abgasgeschwindigkeit wird die Gleichmäßigkeit verbessert, wird sie jedoch zu stark erhöht, nimmt die Gleichmäßigkeit ab. Man erkennt, dass es einen optimalen Wert für die Abgasgeschwindigkeit gibt.
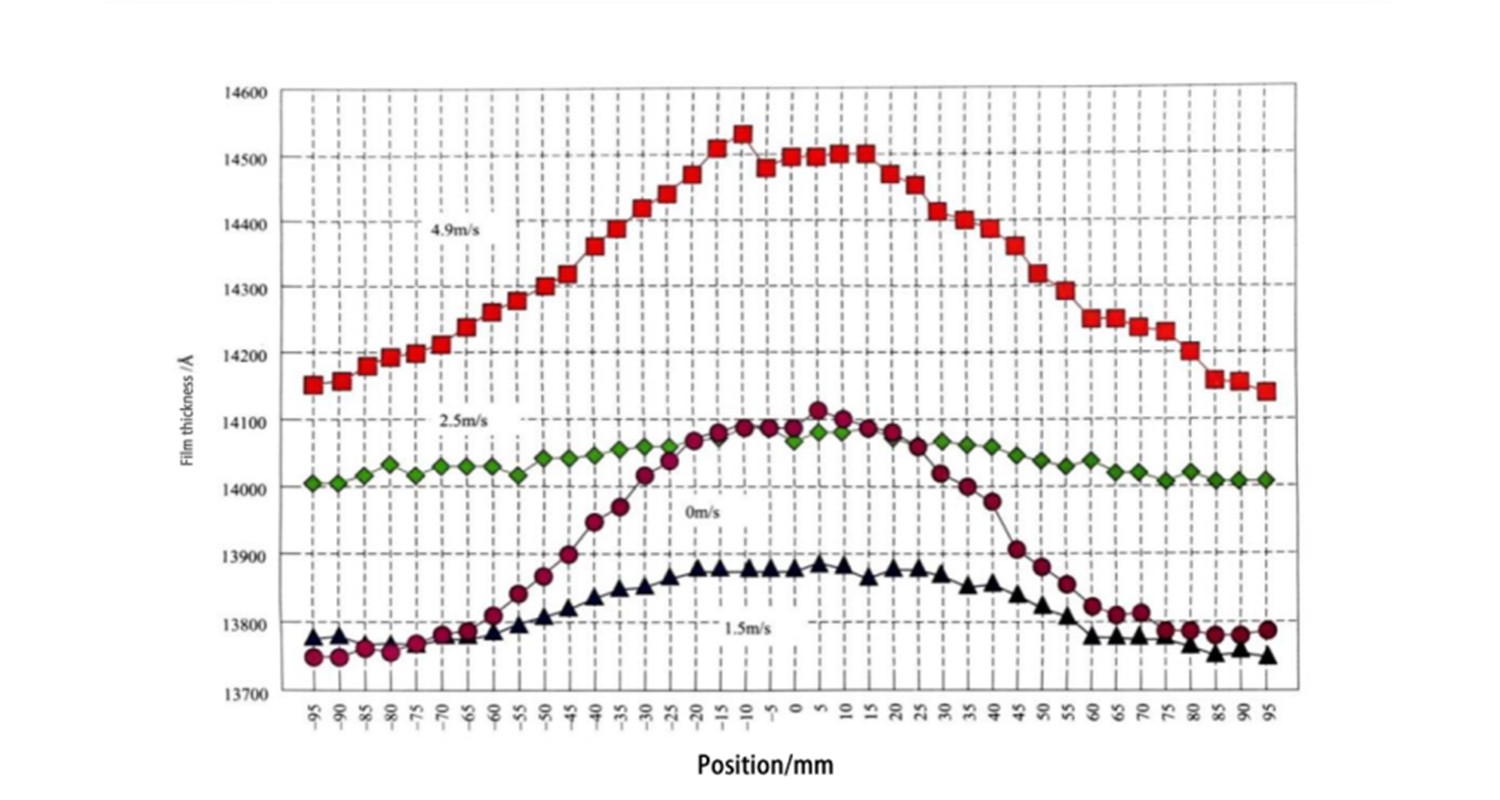
Abbildung 6: Zusammenhang zwischen Abgasgeschwindigkeit und Filmdickenverteilung
HMDS-Behandlung
Um den Fotolack besser beschichtbar zu machen, muss der Wafer mit Hexamethyldisilazan (HMDS) behandelt werden. Insbesondere wenn sich Feuchtigkeit an der Oberfläche des Si-Oxidfilms anlagert, entsteht Silanol, das die Haftung des Fotolacks verringert. Um Feuchtigkeit zu entfernen und Silanol zu zersetzen, wird der Wafer normalerweise auf 100–120 °C erhitzt und HMDS-Nebel eingebracht, um eine chemische Reaktion auszulösen. Der Reaktionsmechanismus ist in Abbildung 7 dargestellt. Durch die HMDS-Behandlung wird die hydrophile Oberfläche mit kleinem Kontaktwinkel zu einer hydrophoben Oberfläche mit großem Kontaktwinkel. Durch Erhitzen des Wafers kann eine höhere Fotolackhaftung erreicht werden.
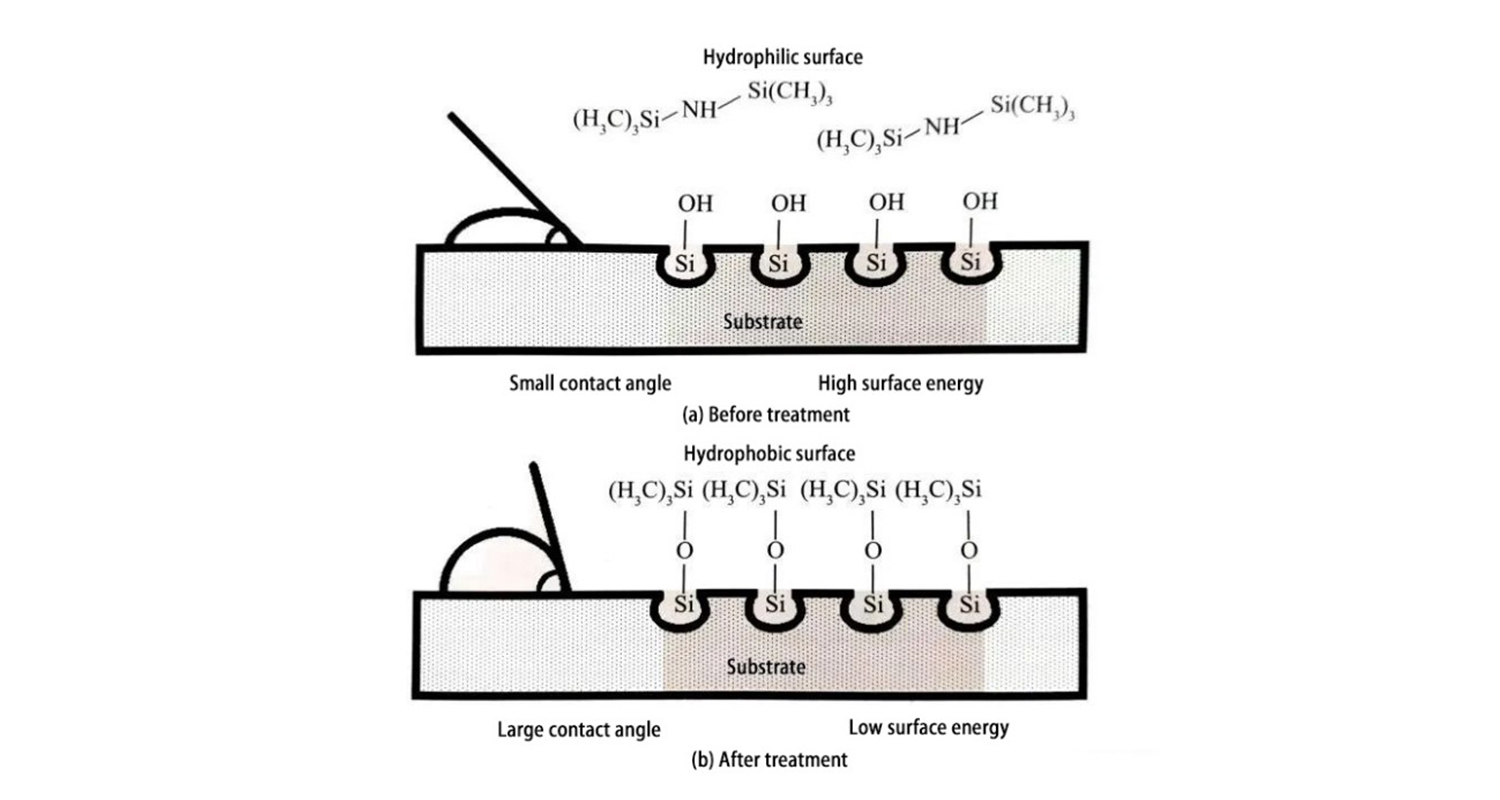
Abbildung 7: HMDS-Reaktionsmechanismus
Der Effekt der HMDS-Behandlung kann durch Messung des Kontaktwinkels beobachtet werden. Abbildung 8 zeigt die Beziehung zwischen HMDS-Behandlungszeit und Kontaktwinkel (Behandlungstemperatur 110 °C). Das Substrat ist Si, die HMDS-Behandlungszeit beträgt mehr als 1 Minute, der Kontaktwinkel ist größer als 80° und der Behandlungseffekt ist stabil. Abbildung 9 zeigt die Beziehung zwischen der HMDS-Behandlungstemperatur und dem Kontaktwinkel (Behandlungszeit 60 s). Wenn die Temperatur 120 °C überschreitet, nimmt der Kontaktwinkel ab, was darauf hindeutet, dass sich HMDS durch Hitze zersetzt. Daher wird die HMDS-Behandlung normalerweise bei 100–110 °C durchgeführt.
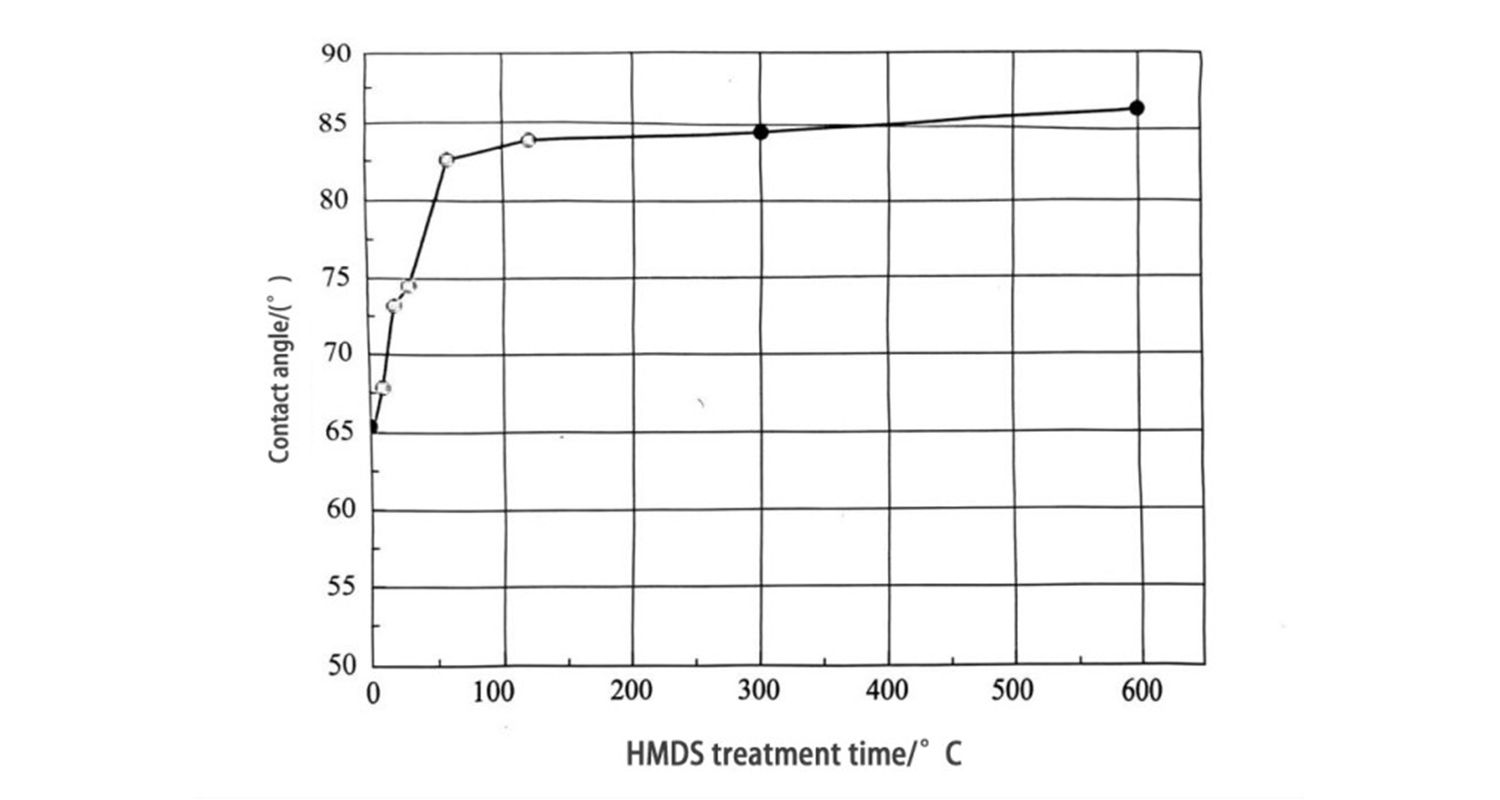
Abbildung 8: Zusammenhang zwischen der HMDS-Behandlungszeit
und Kontaktwinkel (Behandlungstemperatur 110℃)
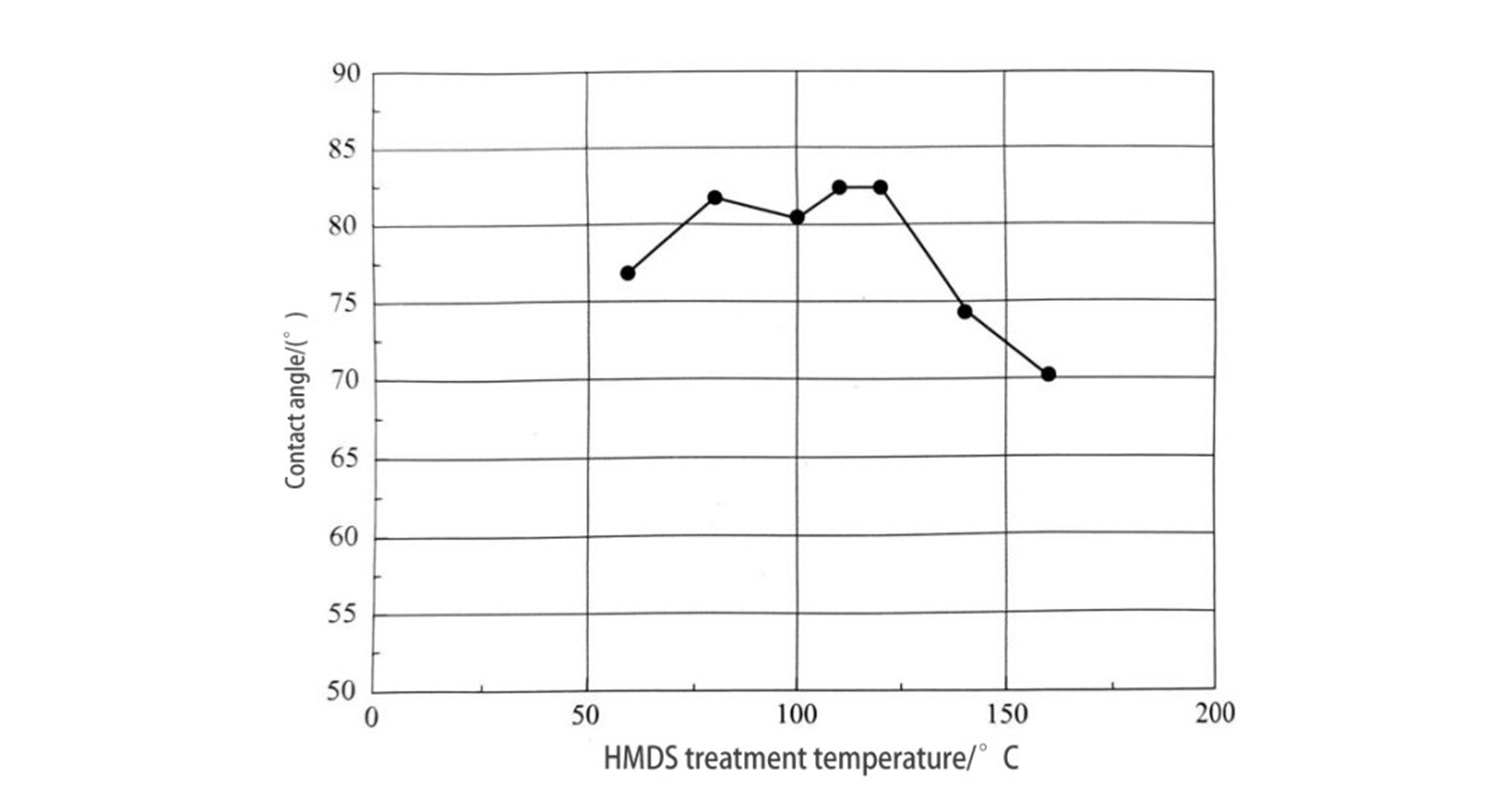
Abbildung 9: Zusammenhang zwischen HMDS-Behandlungstemperatur und Kontaktwinkel (Behandlungszeit 60 s)
Die HMDS-Behandlung wird auf einem Siliziumsubstrat mit einem Oxidfilm durchgeführt, um ein Fotolackmuster zu bilden. Der Oxidfilm wird dann mit Flusssäure unter Zugabe eines Puffers geätzt, und es wurde festgestellt, dass nach der HMDS-Behandlung verhindert werden kann, dass das Photoresistmuster abfällt. Abbildung 10 zeigt die Wirkung der HMDS-Behandlung (Mustergröße beträgt 1 µm).
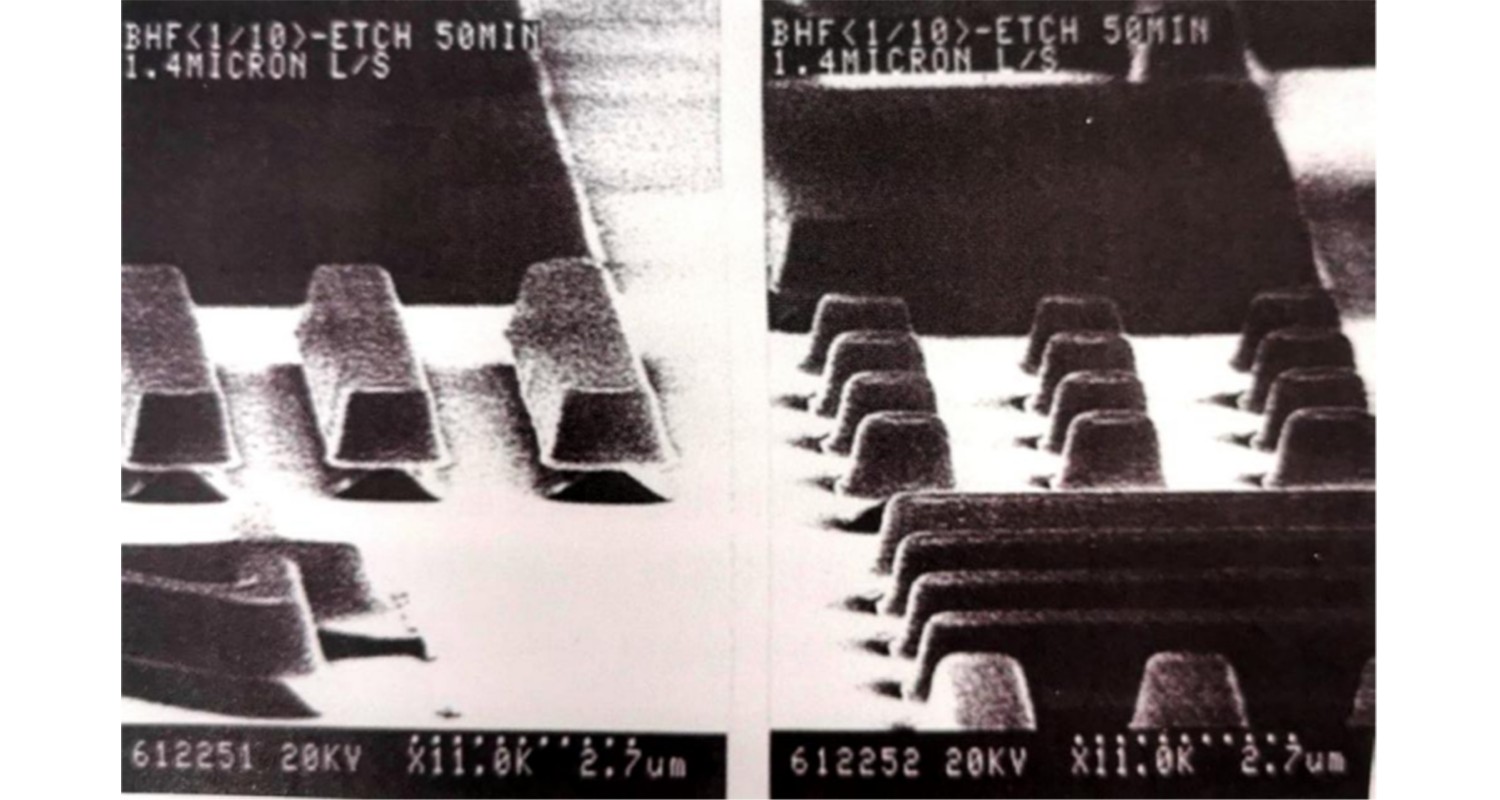
Abbildung 10: HMDS-Behandlungseffekt (Mustergröße beträgt 1 µm)
Vorbacken
Bei gleicher Rotationsgeschwindigkeit ist die Filmdicke umso geringer, je höher die Vorbacktemperatur ist. Dies bedeutet, dass je höher die Vorbacktemperatur ist, desto mehr Lösungsmittel verdunstet, was zu einer geringeren Filmdicke führt. Abbildung 11 zeigt die Beziehung zwischen der Vorbacktemperatur und dem Dill-A-Parameter. Der A-Parameter gibt die Konzentration des lichtempfindlichen Mittels an. Wie aus der Abbildung ersichtlich ist, nimmt der A-Parameter ab, wenn die Vorbacktemperatur auf über 140 °C ansteigt, was darauf hindeutet, dass sich das lichtempfindliche Mittel bei einer höheren Temperatur zersetzt. Abbildung 12 zeigt die spektrale Transmission bei verschiedenen Vorbacktemperaturen. Bei 160°C und 180°C ist eine Erhöhung der Transmission im Wellenlängenbereich von 300-500nm zu beobachten. Dies bestätigt, dass das lichtempfindliche Mittel bei hohen Temperaturen gebacken und zersetzt wird. Die Vorbacktemperatur hat einen optimalen Wert, der durch Lichteigenschaften und Empfindlichkeit bestimmt wird.
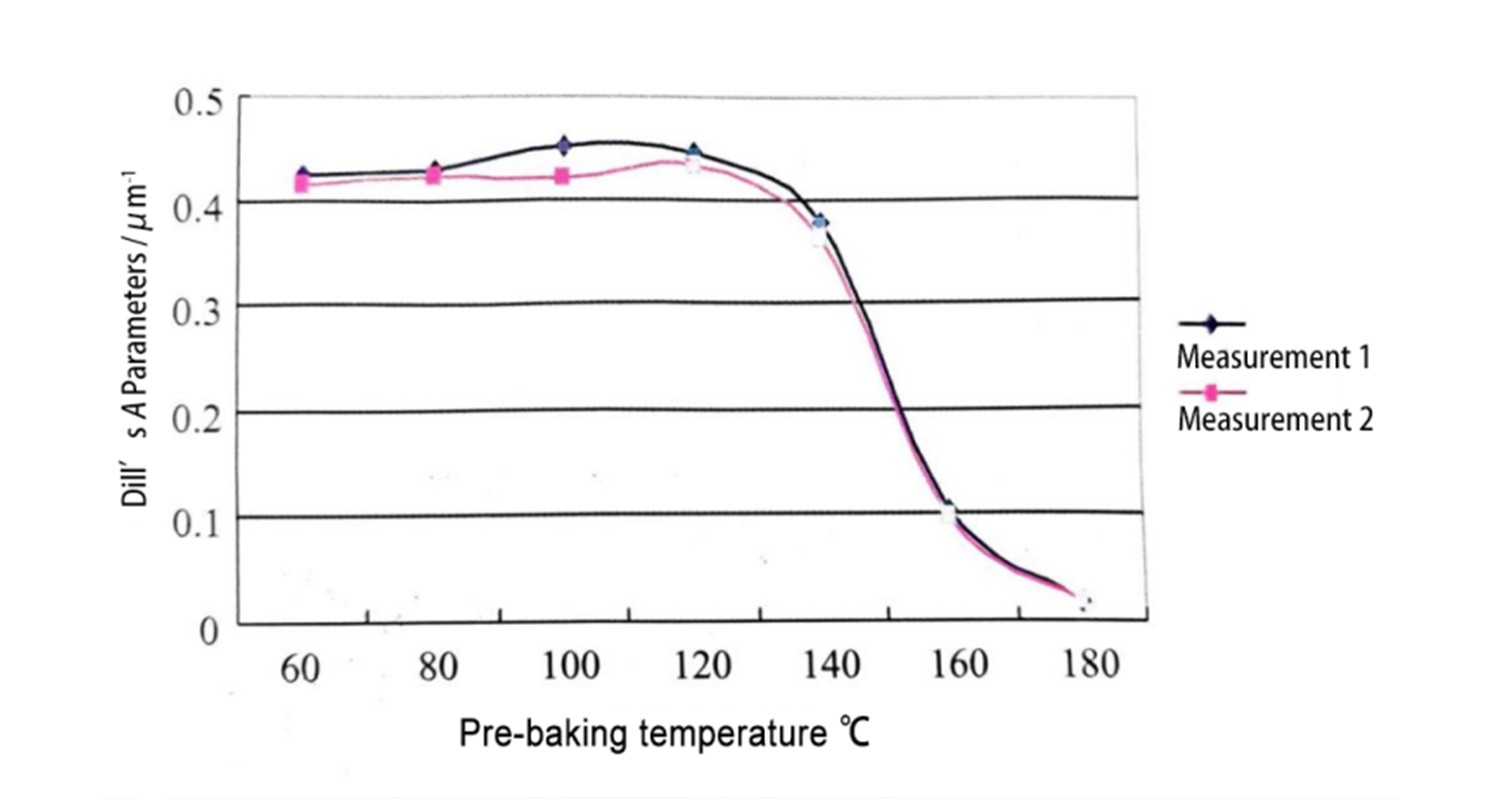
Abbildung 11: Zusammenhang zwischen Vorbacktemperatur und Dill's A-Parameter
(gemessener Wert von OFPR-800/2)
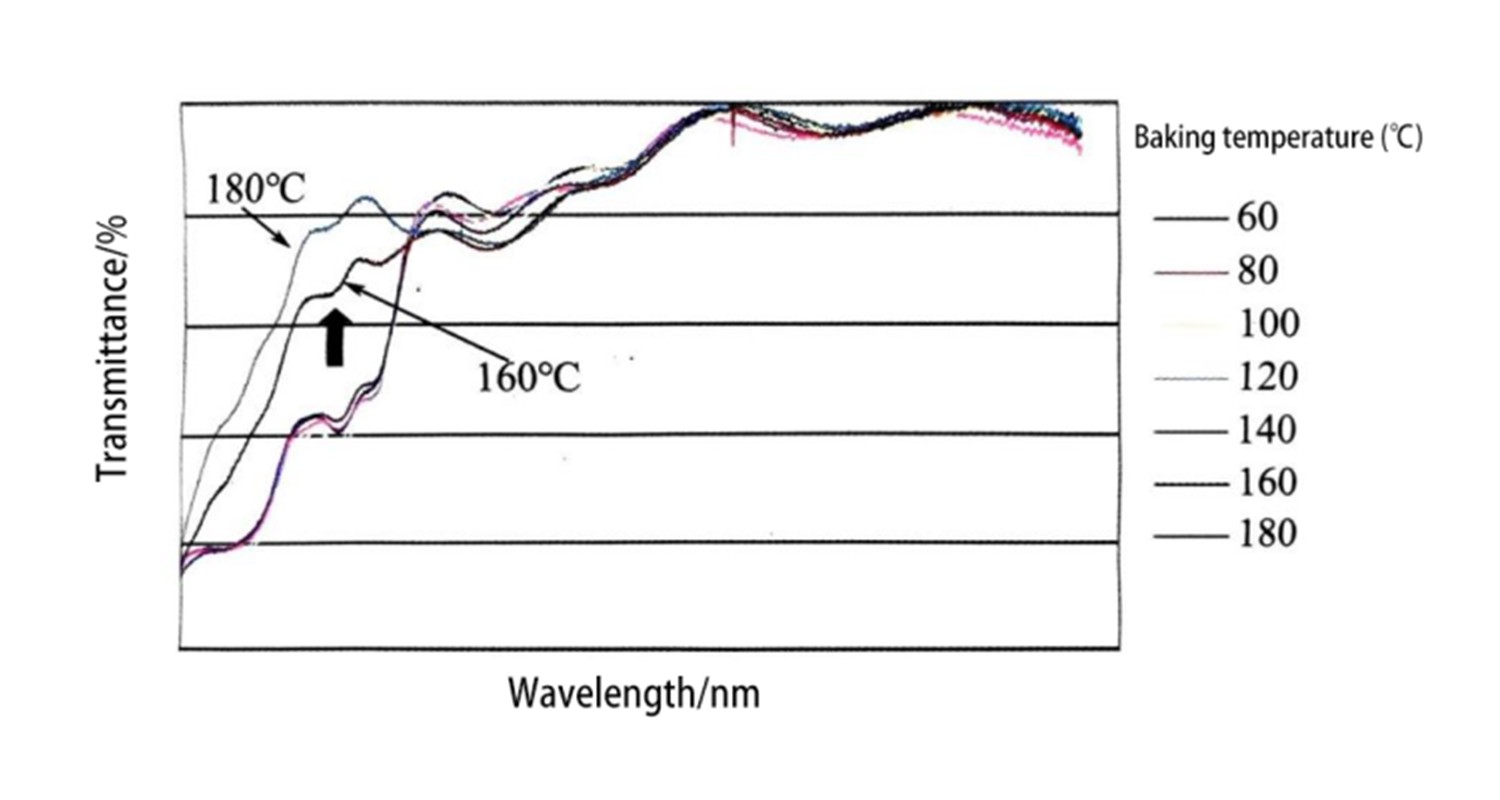
Abbildung 12: Spektrale Transmission bei verschiedenen Vorbacktemperaturen
(OFPR-800, 1 µm Filmdicke)
Kurz gesagt, das Schleuderbeschichtungsverfahren bietet einzigartige Vorteile wie eine präzise Steuerung der Filmdicke, ein hohes Kostenergebnis, milde Prozessbedingungen und eine einfache Bedienung, sodass es erhebliche Auswirkungen auf die Reduzierung der Umweltverschmutzung, die Energieeinsparung und die Verbesserung des Kostenverhaltens hat. In den letzten Jahren hat das Schleuderbeschichten immer mehr an Bedeutung gewonnen und seine Anwendung hat sich nach und nach auf verschiedene Bereiche ausgeweitet.
Zeitpunkt der Veröffentlichung: 27. November 2024